Brass faucets are commonly used in households and commercial settings due to their durability, resistance to corrosion, and appealing aesthetic. In this article, we will explore the production process of brass faucets, from the raw materials to the finished product.
Raw Materials The primary raw materials used in the production of brass faucets are copper and zinc. Copper is the primary constituent of brass, typically making up 60-70% of the alloy, while zinc makes up the remaining 30-40%. Other metals such as lead and tin may also be added to the alloy to enhance specific properties of the brass.
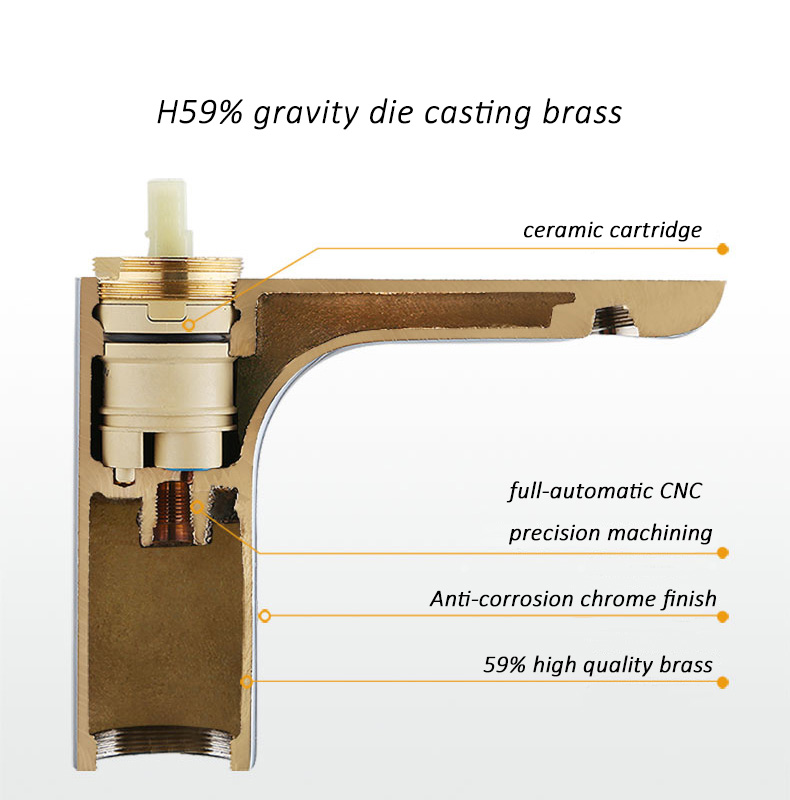
The internal structure of the faucet
Nguyên liệu thô
The primary raw materials used in the production of brass faucets are copper and zinc. Copper is the primary constituent of brass, typically making up 60-70% of the alloy, while zinc makes up the remaining 30-40%. Other metals such as lead and tin may also be added to the alloy to enhance specific properties of the brass.
Production Process The production of brass faucets typically involves the following steps:
1.Melting and Casting.
Casting is a manufacturing process that involves heating metal to a high temperature and then shaping it into the desired form using a die.
The first step in the production process is to melt the copper and zinc in a furnace at high temperatures.
Once the brass has melted, it is poured into a mold to create a bar or billet of brass. This billet is then cooled and stored until it is ready to be used.
To begin the hot forging process, the billet of brass is reheated to a temperature of around 1,800 degrees Fahrenheit. Once the brass has reached the desired temperature, it is placed into a forging press. The forging press applies pressure to the brass, forcing it to take the shape of a die.
The die used to shape the brass is made from steel and is designed to create the specific shape of the faucet.
2.Rough Machining
Once the castings have cooled, they are removed from the molds and undergo rough machining to remove any excess material and give them their basic shape. This is typically done using a lathe or milling machine.
3.Finishing
After rough machining, the castings undergo several stages of finishing to achieve their final shape and surface finish. This may involve further machining, polishing, and buffing.
4.Plating
The final step in the production process is to plate the faucet with a layer of chrome or other decorative metal. This not only enhances the faucet’s appearance but also provides additional protection against corrosion.
5..Assembly
The various components of the faucet, such as the spout, handle, and valve, are then assembled together. This may involve screwing or pressing the parts together or using adhesives to hold them in place.
6.Quality Control
Throughout the production process, quality control measures are put in place to ensure that the faucets meet the required standards. These may include visual inspections, testing for leaks and other defects, and checking the dimensions and tolerances of the various components.
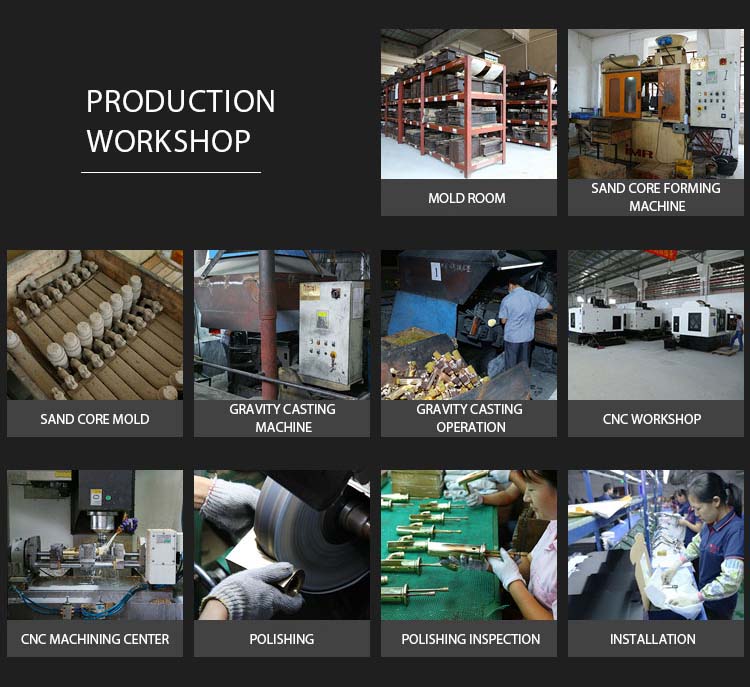
The production process of the faucet
Conclusion
The production of brass faucets involves several stages, from melting the raw materials to plating the finished product to installation. The use of high-quality raw materials, precision manufacturing techniques, and stringent quality control measures all contribute to the production of durable, long-lasting faucets that are both functional and aesthetically pleasing.